کاربرد های مواد کامپوزیت در ناوگان راه آهن
- دانیال عموزاده
نویسندگان این مقاله : M. Robinson, E. Matsika , Q. Peng
چکیده
در اجزای ناوگان ریلی تا به امروز از مواد کامپوزیتی استفاده شده است. در آینده احتمالاً از این نوع دست مواد بیشتر مورد استفاده قرار خواهند گرفت. ناوگان ریلی که به تازگی تولید شده اند به طور معمول از مواد کامپوزیت برای ساخت پروفیلهای سه بعدی پیچیده و پنلهای با نسبت سختی به وزن بالا برای قسمت جلویی کابین و فضای داخلی ناوگان استفاده میکنند.
استفاده از FRP (پلیمرهای تقویتشده با الیاف) به تدریج به سایر قسمت ها برده شد، خواص خاص این ماده ها، عملکرد قابل قبول تر و برتری نسبت به مواد سنتی مانند فولاد و آلومینیوم ارائه می دادند و طی مدت زمانی کاربرد آنها در ناوگان ریلی گسترش یافت. در ناوگان ریلی جدید، کامپوزیتها اغلب اولین انتخاب برای ساخت اجزایی با پروفیلهای سه بعدی پیچیده (مانند قسمت جلوی کابین، صندلیها و دیگر تجهیزات داخلی) و پانلهایی که نیاز به نسبت سختی به وزن بالا دارند، هستند.
علاوه بر این، با توجه به اینکه صنعت راهآهن به طور فزایندهای به اهمیت مسائلی مانند کاهش وزن، هزینههای چرخه عمر(life cycle) و قابلیت تحمل ضربه(crashworthiness) پی برده است، به نظر میرسد که استفاده از کامپوزیتها در سالهای آینده به طور چشمگیری افزایش خواهد یافت. این مقاله به برخی از حوزههایی اشاره میکند که در آنها مجموعههای کامپوزیتی پیشرفته توسط سازمان های راهآهن در سراسر جهان با موفقیت توسعه یافتهاند. همچنین به بررسی موانع استفاده گسترده از کامپوزیتها در ساخت وسایل نقلیه ریلی میپردازد و روشهای اروپایی برای غلبه بر این موانع را نشان خواهد داد.
مقدمه
این مقاله به بررسی اجزای ناوگان ریلی میپردازد که تاکنون از مواد کامپوزیتی بهطور موفقیتآمیز استفاده کرده اند و آنهایی که احتمالاً در آینده نزدیک بیشتر مورد بهرهبرداری قرار خواهند گرفت. بهطور خاص به برخی از ناوگان ریلی امروزی اشاره شده است که بهطور معمول از کامپوزیتها برای ساخت پروفیلهای سهبعدی پیچیده و پانلهایی با نسبت سختی به وزن بالا برای قسمتهای جلوی کابین و فضای داخلی وسایل نقلیه استفاده میکنند. تحقیقات توسط سازمانهای راهآهن در سراسر جهان در حال انجام است تا ساختارهای کامپوزیتی پیشرفتهتری برای بدنهها، بوژیها و مجموعههای چرخ توسعه یابند. مطالعات موردی طراحی، نشان می دهد که استفاده از مواد کامپوزیتی در ساختارهای کابین به بهبود مقاومت بدنه ناوگان در تصادفات منجر می شود.
در مقایسه با صنایع هوافضا، دریایی و خودروسازی، تصور میشود که صنعت راهآهن در پذیرش مواد کامپوزیتی کند عمل کرده است. در حالی که این موضوع تا حدی درست است، اما باید اشاره کرد که این مواد در برخی از قسمت های ناوگان، سالها است که مورد استفاده قرار گرفته اند. در انگلستان، قطارهای حومهای برقی منطقه جنوبی از اوایل دهه ۱۹۵۰ با درهایی که اجزای آنها از GRP (پلاستیک تقویتشده با الیاف شیشه)تولید شده بودند، سیر می کردند. این درها حداقل دو برابر درهای چوبی با روکش فلزی که در آن زمان رایج بود، عمر می کردند.
علاوه بر این، با توجه به اینکه صنعت راهآهن به طور فزایندهای به اهمیت مسائلی مانند کاهش وزن، هزینههای چرخه عمر(life cycle) و قابلیت تحمل ضربه(crashworthiness) پی برده است، به نظر میرسد که استفاده از کامپوزیتها در سالهای آینده به طور چشمگیری افزایش خواهد یافت. این مقاله به برخی از حوزههایی اشاره میکند که در آنها مجموعههای کامپوزیتی پیشرفته توسط سازمان های راهآهن در سراسر جهان با موفقیت توسعه یافتهاند. همچنین به بررسی موانع استفاده گسترده از کامپوزیتها در ساخت وسایل نقلیه ریلی میپردازد و روشهای اروپایی برای غلبه بر این موانع را نشان خواهد داد.
کامپوزیت ها در راه آهن های امروزی
استفاده از کامپوزیتها در ناوگان ریلی در سالهای اخیر به طور قابل توجهی افزایش یافته است، زیرا طراحان به مزایایی این مواد پی بردهاند. در حال حاضر، استفاده از کامپوزیتها در ناوگان ریلی عمدتاً به اجزایی با پروفیلهای سهبعدی پیچیده مانند قسمتهای جلوی کابین، صندلیها و دیگر تجهیزات داخلی و پانلهایی که نیاز به نسبت سختی به وزن بالا دارند، محدود است. در ادامه، به قسمتهای جلوی کابین قطارها، تجهیزات سبک وزن برای فضای داخلی وسایل نقلیه مسافری و پانلها پرداخته میشود.
کابین های قطار
کامپوزیتها به طور گستردهای در قسمتهای جلوی کابین ناوگان ریلی استفاده شدهاند، زیرا پروفیلهای پیچیده سه بعدی مورد نیاز برای بهینهسازی آیرودینامیک و زیباییشناسی قطارهای مدرن میتواند از فلزات هم مشکلساز و هم پرهزینه باشد. با توجه به مزایای حاصل از کاهش وزن و مقاومت در برابر ضربه، باعث افزایش اعتماد تولید کنندگان این صنعت به استفاده از ساختارهای کامپوزیتی خوداتکا (مخصوصا کامپوزیت هایFRPها) منجر شده است.
یکی از نخستین ساختار های کامپوزیتی مورد استفاده در راه آهن را قسمت جلوی کابین قطار سریعالسیر InterCity125 در انگلستان مورد استفاده قرار گرفت که از سال 1977 به خدمت انگلستان درآمد.
ساختار ساندویچی شامل لایههای تقویتشده با GRP (شیشه با الیاف پلاستیک) که دور آن را هسته فوم پلییورتان پوشانده بود، ساخته شد.
لایه بیرونی بهصورت یک قالب یکپارچه تولید شد و لایه داخلی از سه قسمت جداگانه تشکیل شد. سپس این دو لایه بههم پیوسته و بهطور متقابل مونتاژ شدند تا حفرهای ایجاد شود که فوم پلییورتان در آن تزریق شود. علاوه بر این، در ساختار ساندویچی، فضای لازم برای قرار دادن لولهکشیهای مربوط به تهویه مطبوع و سیمکشیهای الکتریکی درنظر گرفته شده بود.
ساختار حاصل حدود 30-35% سبکتر از کابینهای فولادی معمولی تخمین زده شد و دارای مقاومت ضربهای کافی بود تا از نفوذ یک مکعب فولادی 0.9 کیلوگرمی، با سرعت 350 km/h، جلوگیری کند. مطالعات اخیر نشان میدهد که حتی تحت رژیم آزمایش GM/RT2100 کنونی، مواد کامپوزیتی عملکرد خوبی در برابر بارهای ضربهای دارند.
این آزمایش مقاومت در برابر نفوذ را با استفاده از یک سیلندر با آلیاژ آلومینیوم به قطر 94 میلیمتر و نوک نیمکرهای، که وزن آن 1 کیلوگرم است با سرعت حداکثر سرعت عملیاتی وسیله نقلیه بهاضافه 160 km/h حرکت می دهد و مقدار نفوذ آن را به ناوگان می سنجند.
برای نوک قطار سریعالسیر جدیدتر ایتالیایی ETR 500 از ساختار مواد متفاوتی استفاده شد. سرعت 300 km/h نیاز به سختی و مقاومت بیشتری در برابر ضربه دارد که توسط ترکیب الیاف آرامید و رزین اپوکسی فراهم میشد. این مواد قالبگیری شده به یک پروفیل آیرودینامیکی تبدیل شدند که در سرعتهای بالا ثبات ابعادی خوبی دارد. نوک کابین آیرودینامیکی ETR 460 که توسط Sistemi Compositi تولید شده، با استفاده از روش RTM و با الیاف آرامید، شیشه ، رزین پلیاستر مقاوم در برابر آتش و فوم پلییورتان ساخته شد.
38 دستگاه «Le Shuttle» که در تونل ها در حرکت هستند، دارای کابینهایی هستند که نوع دیگری از مواد کامپوزیتی ساخته شدهاند (شکل 2). از آنجا که این ناوگان بیشتر عمر خود را زیرزمین میگذرانند، باید با مقررات بسیار سختگیرانه آتشنشانی مطابقت داشته باشند. به همین دلیل، رزین فنولیک مقاوم در برابر آتش برای استفاده در کابینهای ساخته شده از GRP این وسایل نقلیه انتخاب شده است.
با توجه به اینکه هر قالب اصلی کابین وزن 240 کیلوگرم دارد، قسمتهای جلوی «Le Shuttle» از بزرگترین قالبهای فنولیکی دستی تولید شده تا به امروز هستند. با این حال، با وجود اندازه بزرگشان، کابینها با دقت بالایی تولید شدند و ابعاد قالبگیری شده با تلرانسی در حدود 2 میلیمتر حفظ شد. رزینهای فنولیکی از سال 1985 برای ساخت و بازسازی ناوگان مترو لندن استفاده شدهاند. قسمتهای جلوی کابین تولید شده برای GEC Alstom و در حال حرکت در خطوط شمالی و Jubilee با استفاده از رزینهای فنولیکی ساخته شدهاند.
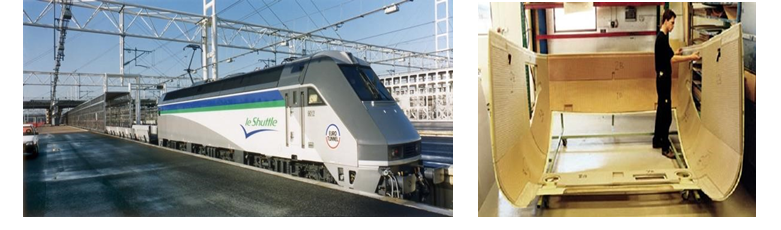
شکل 2: ساختار ساندویچی و لمینتی شکل 1 : لکومتیو le shuttle
قسمتهای جلوی کابین تولید شده برای GEC Alstom و در حال سیر در خطوط شمالی و قطار Jubilee با استفاده از رزینهای فنولیکی ساخته شدند.
این مقاومت لازم در برابر ضربه با استفاده از یک لایه فنولیکی با ضخامت 6 میلیمتر ایجاد شد به دلیل اینکه 30% حرکت این قطار در زیر زمین بود، رزینهای فنولیکی برای سیر در تونل ها انتخاب شدند. در ابتدا، قسمتهای جلوی قطار بهصورت دستی ساخته شدند، اما با پیشرفت پروژه، از فرآیند SCRIMP استفاده شد.
یکی از مثال هایی که نشان میدهد کامپوزیتها اکنون تنها انتخاب معقول برای قسمتهای کابین هستند، واگن مترو C20 استکهلم است.
شکل پیچیده کابین، تولید کنندگان را مجبور به استفاده از مواد کامپوزیتی کرد. برای تبدیل یک ضرورت به یک مزیت، برای اولین بار در یک ناوگان Adtranz Sweden تصمیم گرفته شد که دیوار حمال کابین از جنس کامپوزیت باشد. کابین به گونهای طراحی شد که به استحکام کلی ناوگان کمک کند و در عین حال الزامات ایمنی در برابر آتش برای عملکرد بهینه در تونلها را برآورده کند. کابین راننده یک قالب بزرگ به مساحت حدود 15 مترمربع است که بهصورت دستی و با لایهگذاری تولید شده است.
لایهگذاری دستی به دلیل هزینه پایین، برای تولید اجزای با حجم نسبتاً کم مناسب است (شکل 1). لایههای بیرونی با استفاده از فایبر گلاس با الیاف چندمحوری که در رزین پلیاستر قرار می گیرد پوشانده می شود.برای رعایت الزامات ایمنی در برابر آتش باید به رزین پلیاستر، هیدروکسید آلومینیوم (ATH) اضافه شود تا امکان احتراق آسان آن کمتر و اگر پلی استر اتش گرفت، گاز سمی کمی تولید کند. ماده که به عنوان هسته ی نگهدارنده این کابین استفاده شده چوب بالسا است.
ساختار کابین کامپوزیتی بعد از اتمام فرآیند تولید، به بدنه فولادی واگن پیچ میشود.
در چین، پیشرفتهایی در ساخت کابینها با استفاده از مواد کامپوزیتی در قطار ها صورت گرفته است، همانطور که در شکل 3 نشان داده شده است. یکی از توسعه یافته ترین قطارها، سری CRH که در سمت چپ تصویر قرار دارد و در سال 2011 با سرعت 500km/h آزمایش شد. این قطار شش واگنه با بدنه سرپوشیده مخروطی در فرایند ساخت بدنه از موادCFRP (پلاستیکی تقویتشده با الیاف کربن) استفاده میکند (به شکل 3 مراجعه کنید).
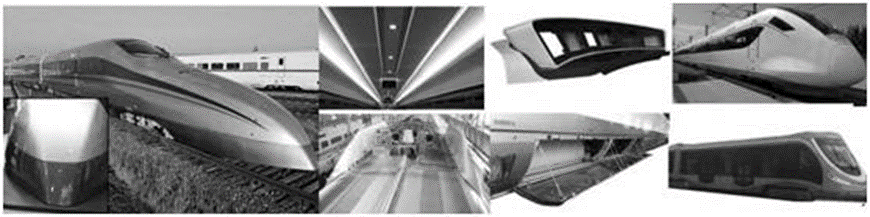
شکل 3: بخش های از قطار های سری CHR که از CFRP استفاده می کنند.
قطعات داخلی قطار
الزامات کاهش وزن و سهولت در ساخت، منجر به استفاده گسترده از مواد کامپوزیتی در فضای داخلی وسایل نقلیه ریلی شده است. در واقع، مواد FRP تقریباً 8٪ (حدود 3 تن) از وزن کل یک واگن مسافری intercity را تشکیل میدهند. به طور کلی، رایجترین مواد کامپوزیتی که برای تجهیزات داخلی استفاده شده است، الیاف شیشه در یک رزین پلیاستر مقاوم در برابر آتش است. لبههای پنجره، توالت ، پانلهای راهروی ورودی و سقفهای انتهایی از قسمت های دیگری هستند که از این مواد استفاده شده است که به صورت سرد پرس شده اند، اسپری شده اند یا به صورت دستی لایهگذاری شدهاند. در مواردی که تولیدات بزرگ توجیهگر هزینههای بالای ابزارآلات مرتبط هستند، پرس گرم ورق قالبگیری شده (SMC) برای ساخت پوستههای صندلی مسافران استفاده شده است (شکل 5). به همین ترتیب، روش RTM کاربرد فزایندهای پیدا کرده است؛ ناوگان سبک ریلی استراسبورگ دارای اجزای صندلی و درهای کشویی هستند که با این فرآیند ساخته شدهاند.
علاوه بر اجزای قالبگیری شده فوق، کامپوزیتها در پنلهای ساندویچی با نسبت استحکام به وزن بالا برای فضای داخلی ناوگان ریلی نیز مورد استفاده قرار گرفتهاند. چنین پنلهایی که معمولاً از یک هسته فوم یا لانه زنبوری بین دو لایه FRP تشکیل شدهاند، برای سالها در صنعت هوافضا استفاده شدهاند. با این حال، با تلاش روزافزون طراحان برای ساخت ناوگان ریلی سبکتر، باعث شده است که کاربرد آنها در واگنهای ریلی در حال گسترش باشد.
قطار سریعالسیر ایتالیایی ETR 500 نمونه خوبی از استفاده از چنین کامپوزیتهایی در یک قطار مدرن با سرعت بالا است، با دیوارهای داخلی، سقفها و محفظههای بار که همگی از پنلهای ساندویچی ساخته شدهاند. این پانل های ساندویچی شامل یک هسته لانه زنبوری بین لایههای شیشهای-فنولیکی است (نمونهای در شکل 4 نشان داده شده است) که با یک لایه پلیوینیل فلوراید پوشانده شده است. این ترکیب وزن سبک از مواد به دلیل تطبیقپذیری و مقاومت مکانیکی بالا انتخاب شده است. به طور مشابه، واگنهای شاتل یوروتانل (Eurotunnel’s tourist shuttle) از پنلهای لانه زنبوری فنولیکی برای بدنههای داخلی خود استفاده میکنند.
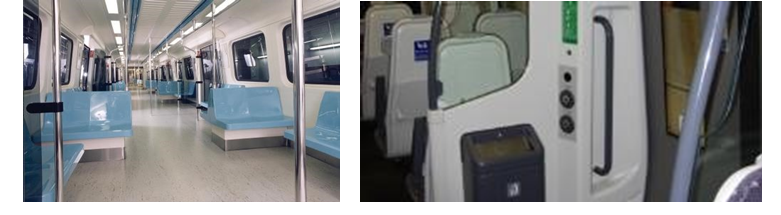
شکل 5:کاربرد های کامپوزیت فنولیک شکل4: ترکیب قالبگیری ورق
تا به امروز، بازار حمل و نقل عمومی بهعنوان مهمترین بازار برای کامپوزیتهای فنولیکی شناخته شده است. در سال 1994، مشکلی با قطعات داخلی ترموپلاستیک به وجود آمد که تحت تأثیر تنشهای محیطی ترک خورده بودند. جایگزین این مواد کامپوزیت فنولیکی بودند؛ دلیل این انتخاب، مقاومت در برابر آتش سوزی، کاهش وزن و مقاومت در برابر شرایط محیطی بود. مجموعهای از قالبهای پنل برای قسمتهای انتهایی، جانبی، درها و قفسههای چمدان با استفاده از روش لایهگذاری دستی تولید شدند. سقفها نیز با پاشش الیاف و رزین روی یک هسته فنولیکی برای ایجاد یک ساختار ساندویچی سبکوزن طراحی شدند.
در چین اخیراً شاهد افزایش استفاده از کامپوزیتها برای قسمت های داخلی ناوگان بوده است،تا جایی که تیرها و پنلها از مواد CFRP و GFRP ساخته شده اند، نمونههایی از این موارد در شکل 6 نشان داده شده است.
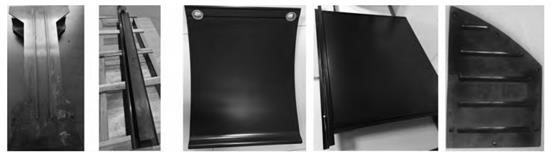
شکل 6: تیر ها و پانل های ساخته شده از مواد کامپوزیت
پانل های سبک
پنلهای کامپوزیتی سبک اما مستحکم معمولاً از یک هسته فومی یا لانه زنبوری تشکیل شدهاند و بین دو لایه تقویتشده با الیاف قرار میگیرند، از اوایل دهه 1970 با موفقیت در صنعت هواپیما به کار گرفته شدهاند. با این حال، با تلاش روزافزون طراحان برای ساخت ناوگان ریلی سبکتر، استفاده از این پنلها در واگنهای راهآهن بهطور فزایندهای در حال گسترش است.
قطار سریعالسیر ETR 500 بار دیگر مثالی عالی از استفاده از کامپوزیتها در یک قطار مدرن با سرعت بالا ارائه میدهد، بهطوری که تمام تجهیزات داخلی آن (دیوارهای جانبی، سقفها، و محفظههای بار) از پنلهای ساندویچی ساخته شدهاند. این ساندویچ شامل یک هسته لانه زنبوری NOMEX است که بین دو لایه شیشهای-فنولیکی لمینت شده قرار گرفته و با یک فیلم PVC Tedlar طراحی شده است. این ساختار به دلیل مقاومت مکانیکی بالا، سبکی و انعطافپذیری ساختاری انتخاب شده است.
در آلمان، تمام پنلهای بیرونی برای شاتل ریجیو(Regio Shuttle) که توسط Adtranz تولید شدهاند، بر اساس لایههای فنولیکی ساخته شدهاند که دور هسته از فوم پلیوینیل کلراید (PVC) قرار گرفته است. این پنلها با استفاده از چسب الاستومری به یک فریم آلومینیومی جوشداده شده است. چون این پنلهای کامپوزیتی باری تحمل نمی کنند ، فومی با وزن کم انتخاب شده است. رزین فنولیک به عنوان گزینه ترجیحی برای رعایت استاندارد آتشسوزی آلمان DIN 5510 بخش 2 انتخاب شد. پرداختکاری سطحی این پنلها با استفاده از یک خمیر سطحی پرکننده قبل از رنگ زدن روی آن قرار خواهد گرفت.
شرکت دانمارکی LM Glasfiber سقفهایی برای قطارهای Talent تولید میکند که از یک ساختار ساندویچی کامپوزیتی استفاده میکنند. دلیل نیاز به وزن سبک برای قطار Talent از سقف کامپوزیتی استفاده شده است. قطار سبکوزن به دلیل کاهش مصرف انرژی و کاهش تأثیرات زیستمحیطی مورد توجه قرار گرفته است. سقف به صورت یک ساختار ساندویچی خود نگهدار ساخته شده و از پلیاستر تقویتشده با شیشه با یک هسته فوم PVC تشکیل شده است. سقف با استفاده از تکنیک تزریق تحت خلا تولید میشود که حجمی از الیاف را ایجاد میکند. هسته در یک قالب بزرگ با یک لایه ژل پلیاستر قرار داده میشود که ظاهر و رنگ خارجی سقف را فراهم میکند. سپس با یک کیسه خلأ پوشانده شده و پلیاستر تحت خلا به داخل قالب کشیده میشود. سقفها در دو بخش به عرض 1.75 متر و طول 7.5 متر قالبگیری شده و با استفاده از چسب به بدنه متصل میشوند. این ساختار با الزامات آتشسوزی DIN 5510 مطابقت دارد. قطار Talent شرکت Talbot اولین قطاری بود که از دیوارهای جانبی به روش پلترودینگ (پلترودینگ یک فرآیند پیوسته است که در آن دستههای الیاف یا تارهای بافته شده با رزینی، که معمولاً از پلییورتان یا اپوکسی تشکیل شده است، آغشته میشوند و سپس از یک قالب گرم عبور داده میشوند که در آن پلیمر شدن رزین اتفاق میافتد . کامپوزیت حاصل سپس به طول مورد نظر بریده میشود.) استفاده کرد.
کاهش وزن و حفاظت در برابر آتش نیز در چین بهعنوان الزامات طراحی حیاتی شناخته شدهاند. به طبع این امر، بخشی از تحقیقات اکنون بر توسعه پنلهایی متمرکز است که هر دو نیاز را برآورده میکنند، نمونهای از این پنلها در شکل 7 نشان داده شده است.
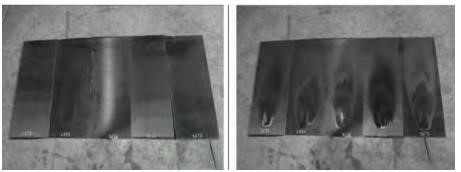
شکل 6: پانل های مقاوم به آتش سوزی
کامپوزیت های در آینده راه آهن
بخش قبلی برخی از حوزههایی را که در آنها مواد کامپوزیتی در صنعت راهآهن بهطور اثبات شده مورد استفاده قرار گرفته و بهطور معمول به کار میروند بحث شد. این بخش به برخی از تحقیقات و توسعههای اخیر میپردازد که سعی کردهاند استفاده از کامپوزیتها را به جنبههای دیگر مهندسی راهآهن که فلزات در آنها جایگاه سنتی قوی دارند، گسترش دهند. استفاده از کامپوزیتها در صنعت راهآهن در حال گسترش است و استفاده از آنها برای ساختارهای تحت فشار بهطور معمول در حال افزایش است زیرا ساختارهای کامپوزیتی طی زمان بهبود یافته و بهتر شده است است. پس از استفاده برجسته از کامپوزیتها در پوستههای بدنه واگنهای مسافری با الیاف پیچیده توسط Schindler Waggon در حال تحقیق است.
اروپا و ژاپن در بهکارگیری کامپوزیتها در قطارهای مسافری پیشرو هستند؛ در آمریکا، ناوگان باری و اجزای ریل، بهویژه پد های زیر ریل تحقیقاتی صورت گرفته است . در بسیاری از تحقیقات کنونی نیاز به مواد کامپوزیتی سبک و در عین حال جذبکننده انرژی است برای لکومتیو ها ضروری دانسته شده و نیاز است جایگزین ساختارهای فلزی سنتی ساخته شده از فولاد یا آلومینیوم شوند.
بهطور کلی، فلزات پرهزینه هستند و نیاز به تعداد زیادی نیرو کار برای تشکیل یک ساختار است،.
فلزات همچنین به دلیل عمر پایین در طول مدت طولانی هزینه بالاتری نسبت به کامپوزیت خواهد داشت ، در حالی که کامپوزیتها میتوانند کاهش وزن تا 50% را ارائه دهند. علاوه بر این، کامپوزیتها دارای خواص غیرخورنده هستند که عمر طولانیتری نسبت به فلزات ارائه خواهند داد. مواد کامپوزیتی انعطافپذیریی را ارائه میدهند که میتواند اشکال پیچیده مورد نیاز بهدلیل ملاحظات آیرودینامیکی و ارگونومیکی را شکل دهد. کامپوزیتها نه تنها باید انرژی را جذب کنند، بلکه باید مقرون به صرفه باشند و تحقیقات نشان داده است که کامپوزیتهای فیبرگلاس استاندارد میتوانند بهطور نوآورانه طراحی شوند تا سطح انرژی بالایی را جذب کنند. دیدگاه سنتی که ساختارهای سبکوزن تحمل ضربات با انرژی بالا را ندارند به شدت توسط طراحان کامپوزیت در تمامی بخشهای حملونقل به چالش کشیده شده است.
بدنه
بدنه یک وسیله نقلیه ریلی سهم قابل توجهی از جرم و هزینههای تولید آن را به خود اختصاص میدهد. با توجه به این که روشهای تولید مواد سنتی مانند فولاد و آلومینیوم به خوبی توسعه یافته است، توجه به طور فزایندهای به استفاده از کامپوزیتها معطوف شده است تا به صرفهجوییهای بیشتری در این زمینهها دست یابند. یکی از هیجانانگیزترین توسعههای اخیر در زمینه ساخت بدنه، توسط شرکت سوئیسی Schindler Waggon در می 1995 رونمایی شد. قطار سه واگنه آن دارای بدنهای است که بهطور کامل از کامپوزیتها ساخته شده و از یک فرآیند تولید خودکار پیشرفته استفاده میکند.
Schindler Waggon مزایای بدنه کامپوزیتی جدید خود را به شرح زیر ذکر میکند: فرآیند تولید تقریباً خودکار، تعداد قطعات بسیار کاهش یافته، مجاری یکپارچه برای کابلها و سیستمهای تهویه، مقاومت عالی در برابر خوردگی، و صرفهجویی در هزینههای چرخه عمر به دلیل کاهش یافته همچنبن، وزن و بهبود عایق حرارتی. با استفاده از امکانات موجود خود، Schindler Waggon میتواند یک بدنه کامل را در 8 روز تکمیل کند. با این حال، پس از پذیرش و اثبات این فناوری، آنها برنامههایی برای ظرفیت آینده 200 بدنه در سال دارند. همچنین، ماژولهای داخلی برای وسایل نقلیه بازسازی شده نیز با استفاده از این تکنیک تولید شدهاند.
مهندسان راهآهن در ژاپن نیز به بررسی روشهای کاهش وزن بدنه از طریق استفاده از کامپوزیتهای تقویتشده با الیاف (FRP) پرداختهاند. با این حال، به جای پذیرش رویکرد کاملاً کامپوزیتی Schindler Waggon، شرکت Tokyo Car Corporation و شرکت راهآهن شرق ژاپن به تحقیق در مورد ادغام پوستههای سقف تقویتشده با الیاف کربن (CFRP) در ساختارهای عمدتاً آلومینیومی با استفاده از یک اتصال جوش جدید پرداختهاند. آزمایشها نشان دادهاند که بدنههای قطار با این نوع پوستههای سقف قادر به تحمل نوسانات فشار بالاتری هستند، مرکز ثقل پایینتری دارند و هر وسیله نقلیه حدود 300–500 کیلوگرم سبکتر خواهد شد.
به طور مشابه، موسسه تحقیقات فنی راهآهن ژاپن ساختارهای ترکیبی آلومینیوم-CFRP را توسعه داده و آزمایش کرده است. برای کاهش هزینههای تولید، از فرآیند اتوماسیون پلترودینگ برای تولید پنلهای CFRP استفاده شد. این پنلها سپس به یک چارچوب آلومینیومی با رینگهای چسبانده شده تا ساختار بدنه تکمیل شود. به عنوان توسعهای از این کار، دو نیمه بخش منحنی 1 متری با تقویت یکپارچه از CFRP با استفاده از فرآیند اتوکلاو( توکلاو کردن یک روش تغییر در خواص فیزیکی، شیمیایی یا بیولوژیکی اجسام است که از حرارت مرطوب (بخار) یا حرارت خشک (هوای داغ) همراه با فشار استفاده می کند. فرآیند اتوکلاو بر اساس این مفهوم عمل می کند که تأثیر حرارت روی اجسام، زمانی که تحت فشار هستند افزایش می یابد.) تولید شد. سپس این دو نیمه به هم بسته شده تا یک بخش کامل بدنه را تشکیل دهند که تقریباً 30% سبکتر از یک ساختار آلومینیومی خواهد بود.
به طور مشابه، شرکت ANF Industrie بخشی از Bombardier Eurorail با همکاری دانشگاه، تولید یک مدل پنجم مقیاس از بدنه یک واگن مترو ساختهشده از پوستههای شیشه/اپوکسی در اطراف یک هسته فوم پلیاورتان را انجام دادهاند. اگرچه این طراحی هنوز در مراحل اولیه خود قرار داشت، اما تحلیلهای استاتیکی با استفاده از تکنیکهای تجربی و اجزای محدود نتایج امیدوارکنندهای به دست آورده شد.
در حالی که بدنههای فوقالذکر هنوز وارد تست های عملی نشده اند، واگنهای مونوریل در مجتمع Walt Disney World در فلوریدا از اوایل دهه 1990 با بدنههای کامپوزیتی در حال کار هستند. برای افزایش ظرفیت حمل مسافر سیستم، بدنههای واگنها با استفاده از انواع مواد و ساختار ها مانند شبکه شش ضلعی(شبکه لانه زنبوری)، الیاف فایبرگلاس و رزینهای اپوکسی و فنولیک بازطراحی شدند. وزن بدنههای کامپوزیتی در مقایسه با ساختار آلومینیومی سنتی بیش از 40% کاهش یافت و به دلیل کاهش هزینههای نیروی کار و ضایعات تخمین زده شده که این بدنهها در واقع 9% ارزانتر از طراحی رقیب آلومینیومی هستند.
بوژی
این متن به خوبی اهمیت بوژیها در عملکرد قطارها و مزایای استفاده از مواد مرکب FRP در ساختار بوژیها را توضیح میدهد. در اینجا، بر مزایای وزن کمتر، استحکام بالا، و مقاومت در برابر خوردگی این مواد تأکید شده است که باعث شده تحقیقات و توسعههایی در کشورهای مختلف برای استفاده از این مواد در بوژیها صورت گیرد.
همچنین، مثالهایی از استفاده موفقیتآمیز این فناوری ارائه شده است، مانند واگن بینشهری آلمانی که با قابهای بوژی FRP مجهز شده و در سال 1988 با موفقیت وارد خدمت شده است. این واگن، علاوه بر کاهش وزن قابلتوجه، در طول عمر خود بیش از یک میلیون کیلومتر مسافت را پیموده و از نظر استحکام و عملکرد بهتر از بوژیهای معمولی بوده است.
در نهایت، به مفاهیم رادیکال دیگری مانند قاب و سیستم تعلیق کاملاً کامپوزیت اشاره شده که به عنوان بخشی از پروژه EUREKA Eurobogie طراحی شده است، که نشاندهنده پتانسیل بیشتر این فناوری برای بهبود عملکرد و کاهش هزینهها در صنعت ریلی است.

شکل 8: بوژی کامپوزیتی که زیر نظر شرکت EUREKA Eurobogie
مؤسسه تحقیقات فنی راهآهن ژاپن نیز تحقیقات گستردهای بر روی قابهای بوژی FRP انجام داده است. با استفاده از CFRP (پلیمرهای تقویتشده با الیاف کربن)، موفق به کاهش وزن تا 70 درصد در مقایسه با قابهای ساخته شده از فولاد معمولی شدهاند. همچنین، گزارشها حاکی از آن است که دستیابی به یک پیشرفت فنی برای کاربرد عملی این فناوری نزدیک است.
بهطور مشابه، شرکت ملی راهآهن فرانسه (SNCF) و ‘École Supérieure des Arts et Metiers’ اخیراً یک نمونه اولیه بوژی در مقیاس نصفه تولید کردهاند که دارای شاسی یکپارچهای است که از لایههای الیاف شیشهای/اپوکسی لمینت شده ساخته شده است. این نمونه اولیه دو سوم سبکتر از یک شاسی فلزی معمولی است، مقاومت خستگی بهتری دارد و تعداد قطعات آن به طور قابلتوجهی کاهش یافته است.
چرخ و محور
محققان آلمانی در موسسه ابزارهای ماشینی و مهندسی محصول (IWF) به بررسی استفاده از مواد مرکب برای چرخهای ناوگان ریلی پرداختهاند. این چرخها از CFRP (پلیمرهای تقویتشده با الیاف کربن) ساخته شدهاند که روی یک هسته فومی قالبگیری شده قرار میگیرند و به کاهش وزن تا 50٪ منجر شدهاند، در حالی که همچنان استحکام لازم برای تحمل بارهای برابر با چرخ های فولادی را دارند.
در بریتانیا، راهآهن بریتانیا در طول توسعه قطار پیشرفته مسافری (APT) به بررسی استفاده از CFRP برای محور ناوگان ریلی پرداختند. این محور ها با روش تزریق رزین و پیچیدن فیلامنت ساخته شدند و حدود 70٪ صرفهجویی در وزن نسبت به قطعات فولادی معادل داشتند. با این حال، اگرچه عملکرد استاتیکی و خستگی این لولهها رضایتبخش بود، اما رفتار آنها در برابر ضربه بسیار ضعیف بود و در نتیجه این پروژه کنار گذاشته شد. با این وجود، پیشنهاد شد که این مشکل میتواند با استفاده از ترکیبات مرکب هیبریدی یا با استفاده از محافظها برطرف شود.
پانتوگراف
برای قطارهای الکتریکی که برق خود را از خطوط بالاسری دریافت میکنند، استفاده از مواد مرکب برای ساخت پانتوگراف (چارچوب مفصلی و خودتنظیمی که روی ناوگان قرار دارد و جریان برق را از خطوط بالاسری منتقل میکند) مورد بررسی قرار گرفته است. کارهای اولیه توسط راهآهن بریتانیا بر روی استفاده از CFRP (پلیمر تقویتشده با الیاف کربن) برای سر پانتوگراف متمرکز بود، اما به زودی مشخص شد که این ماده در محیطهایی با ولتاژ بالا عملکرد خوبی ندارد و به شدت دچار فرسایش میشود. در نتیجه، پلاستیک تقویتشده با الیاف آرامید به عنوان جایگزین انتخاب شد و عملکرد رضایتبخشی از خود نشان داد. قطعات نمونه با استفاده از تکنیک کیسه خلاء ساخته شدند و به کاهش وزن 37٪ منجر شدند.
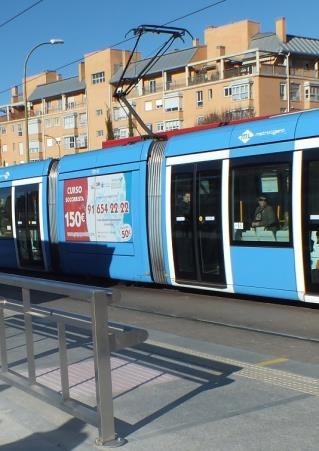
شکل 9: پانتوگراف
نتیجه گیری
این مقاله نشان داده است که مواد کامپوزیتی در راهآهن به خوبی برای اجزای نیمه ساختاری و تجهیزات داخلی جای خود را پیدا کردهاند. با این حال، کاربردهای کامپوزیتهای مبتنی بر الیاف کربن و آرامید تا به امروز محدود بوده است. بدون شک، هزینههای بالای مواد، بهویژه برای الیاف کربن، دلیل اصلی این موضوع بوده است، اما عوامل دیگر نیز مانند عملکرد ضعیف کامپوزیتهای تقویتشده با الیاف کربن در برابر ضربه و استحکام فشاری کم پلاستیکهای تقویتشده با الیاف آرامید نقش دارند. این مشکل با این واقعیت تشدید میشود که برای بهرهبرداری کامل از پتانسیل مواد کامپوزیتی، نیاز به اتخاذ رویکرد طراحی جدید است. با این وجود، مزایایی که میتوان از آنها بهرهمند شد، از نظر انعطافپذیری طراحی، کاهش وزن، هزینههای عمر و غیره، بسیار زیاد است. این واقعیت توسط گستردگی چشمگیر کاربردهایی که برای کامپوزیتها در حال حاضر در نظر گرفته شدهاند، منعکس شده است.
در صنایع ریلی و کامپوزیت، خوشبینی نسبت به آینده برای استفاده از کامپوزیتها در ناوگان ریلی وجود دارد. کامپوزیتها میتوانند بهگونهای مهندسی شوند که بهطور رقابتی با فلزات عمل کنند و بنابراین فرصتهایی برای جایگزینی مستقیم اجزای فلزی با اجزای کامپوزیتی وجود دارد. با این حال، چندین مانع وجود دارد که باید قبل از پذیرش گسترده کامپوزیتها برطرف شوند. به طور کلی، صنعت کامپوزیتها اذعان دارد که نوعی انعطافناپذیری و رکود ذهنی از سوی مسئولان ریلی برای پذیرش طرحهای جدید، ارائه زمانهای آزمایشی کافی و ارائه بازخورد وجود دارد. یک مثال از مشکل معرفی مواد کامپوزیتی به صنعت ریلی این است که برای تأیید این کفپوش کامپوزیتی، لازم است که آن در سیر آزمایش شود و با این حال برای واجد شرایط بودن برای آزمایش در سیر، نیاز به تأیید قبلی دارد! با این وجود، واضح است که صنعت ریلی در قرن بیست و یکم بازار مهمی برای کامپوزیتها خواهد بود، حتی اگر در حال حاضر صنعت ریلی به طور کامل به این موضوع واقف نباشد.
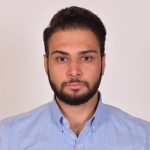